Choosing the right bandsaw blade and running in:
Choosing the right bandsaw blade depends on several factors: the type of the bandsaw and cutting conditions, length and width of the bandsaw blade, number of teeth and tooth form.
Read more about this from our blog post: first steps in choosing the right bandsaw blade, published on August 30, 2017. Each cutting event requires a specific blade and if the right bandsaw blade has been found, follows the correct running in, which considerably prolongs the life of the bandsaw blade. To obtain the maximum blade life, always use the recommended band speed but lower the feed rate by 20-50% during the first 10 minutes of cutting. During the next 10 minutes increase the feed rate in stages, until you have reached the recommended feed rate.
Bandsaw maintenance and the right cutting parameters:
Check the wear and alignment of the guides;
Check the condition and operation of the chip brush;
Check the band tension with a tensionmeter;
Check the band speed with a tachometer;
Upon metal cutting check the coolant concentration with a refractometer. The coolant lubricates, cools and carries the chips from the cut. It is important to use the appropriate cutting fluid and make sure that the cutting fluid reaches the cut with low pressure and large flow.
Make sure that the workpiece is firmly clamped so that is cannot vibrate or rotate. Do not use bent or damaged workpieces.
The right cutting parameters are blade speed and feed rate. Specified blade speed for the type and hardness of the material can be found from the blade speed table. In case of very strong noise or vibration reduce the blade speed by 10-20%. Adjust the feed speed controller to achieve a suitable feed rate. If the material chips are too hot or burned, the feed rate is too high. In case of thin fiber-shaped chips the feed rate is too low.
Instructions for problem solving:
Tooth breakage of the bandsaw blade – tooth pitch too fine; tooth shape too weak; gullets filled, band not properly running in, band speed too low, feed rate too high, workpiece moves, upon metal cutting too little coolant or incorrect concentration.
Rapid tooth wear of the bandsaw blade – tooth pitch too fine, wrong tooth shape selection, chip brush does not work, band not properly running in, band speed too high, feed rate too high or too low, upon metal cutting too little coolant or incorrect concentration, the surface of the cut material is too hard or abrasive or with the surface defects (rust, sand).
Rough surface – guides are loose/worn out/guides too far apart, the parts of the bandsaw have shifted towards the axles, tooth pitch too coarse, band speed too low, feed rate too high, band not properly running in or blade worn out.
Crooked cutting – poorly adjusted guidearm loose/worn out/guide too far apart, tooth pitch too fine, band speed too low, feed rate too high, band tension too low, the bandsaw capacity is not enough, blade worn out.
Band breakage – poorly adjusted guidearm loose/worn out/guide too far apart, tooth pitch too fine, feed rate too high, band tension too high, defective connection to the bandsaw blade.
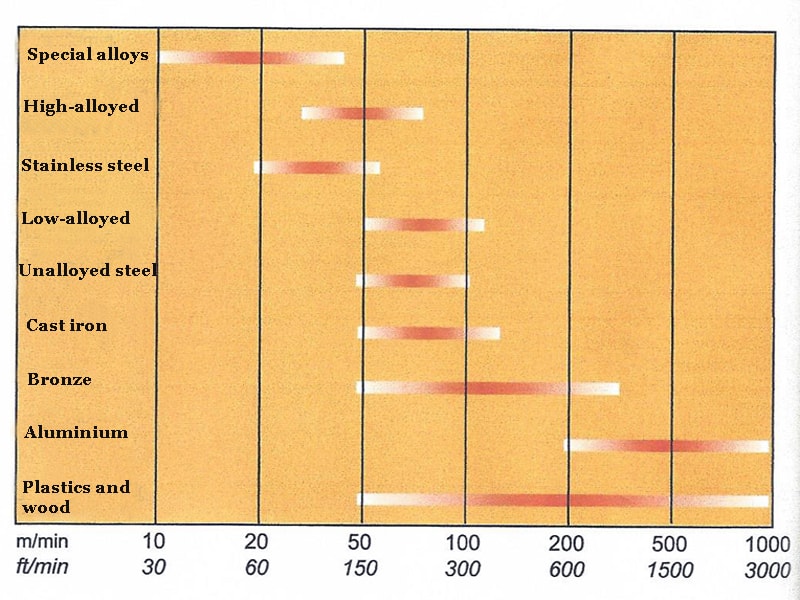